Plates of Lead Acid Battery
Formation of Plates of Lead-acid Cells
There are, in general, two methods of producing the active materials of the cells and attaching them to lead plates. These are known after the names of their inventors.
(1) Plante plates or formed plates
(2) Faure plates or pasted plates.
1. Plante Process
In this process, two sheets of lead are taken and immersed in dilute H2SO4. When a current is passed into this lead-acid cell from a dynamo or some other external source of supply, then due to electrolysis, hydrogen and oxygen are evolved. At anode, oxygen attacks lead converting it into PbO2 whereas cathode is unaffected because hydrogen can form on compound with Pb.
If the cell is now discharged (or current is reversed through it), the peroxide-coated plate becomes cathode, so hydrogen forms on it and combines with the oxygen of PbO2 to form water thus :
PbO2 + 2H2 ⎯→ Pb + 2H2O
At the same time, oxygen goes to anode (the plate previously unattacked) which is lead and reacts to form PbO2. Hence, the anode becomes covered with a thin film of PbO2.
By continuous reversal of the current or by charging and discharging the above electrolytic cell, the thin film of PbO2 will become thicker and thicker and the polarity of the cell will take increasingly longer time to reverse. Two lead plates after being subjected to hundreds of reversals will acquire a skin of PbO2 thick enough to possess sufficiently high capacity. This process of making positive plates is known as formation. The negative plates are also made by the same process. They are turned from positive to negative plates by reversing the current through them until whole PbO2 is converted into sponge lead. Although Plante positives are very commonly used for stationary work, Plante negatives have been completely replaced by the Faure or pasted type plates as discussed in paragraph Faure Process. However, owing to the length of time required and enormous expenditure of electrical energy, this process is commercially impracticable. The process of formation can be accelerated by forming agents such as acetic, nitric or hydrochloric acid or their salts but still this method is expensive and slow and plates are heavy.
2. Structure of Plante Plates
It is seen that since active material on a Plante plate consists of a thin layer of PbO2 formed on and from the surface of the lead plate, it must be made of large superficial area in order to get an appreciable volume of it. An ordinary lead plate subjected to the forming process as discussed above will have very small capacity. Its superficial area and hence its capacity, can be increased by grooving or laminating. Fig. (A) shows a Plante positive plate which consists of a pure lead grid with finely laminated surfaces. The construction of these plates consists of a large number of thin vertical laminations which are strengthened at intervals by horizontal binding ribs. This results in an increase of the superifical area 10 to 12 times that possessed by a plain lead sheet of the same overall dimensions.
The above design makes possible the expansion of the plate structure to accommodate the increase in mass and the value of the active material (PbO2) which takes place when the cell goes through a series of chemical changes during each cycle of charge or discharge. The expansions of the plate structure takes place downwards where there is room left for such purpose. Usually, a Plante positive plate expands by about 10% or so of its length during the course of its useful life.

AdBlock-2
Another type of Plante positive plate is the ‘rosette’ plate which consists of a perforated cast grid or framework of lead alloy with 5 to 12 per cent of antimony holding rosettes or spirals of corrugated pure lead tape. The rosettes (Fig. B) provide the active material of the positive plate and, during formation, they expand in the holes of the grid which are countersunk on both sides of the grid. The advantages of such plates are that the lead-antimony grid is itself unaffected by the chemical action and the complete plate is exceptionally strong.
Other things being equal, the life of a Plante plate is in direct proportion to the weight of lead metal in it, because as the original layer of PbO2 slowly crumbles away during the routing charging and discharging of the cell, fresh active material is formed out of the underlying lead metal. Hence, the capacity of such a plate lasts as long as the plate itself. In this respect, Plante plate is superior to the Faure or pasted plate.

3. Faure Process
In the making of Faure plates, the active material is mechanically applied instead of being electrochemically produced out of lead plate itself as in Plante process. The active material which is in the form of red lead (Pb3O4) or litharge PbO or the mixture of the two in various proportions, is pressed into the interstices of a thin lead grid or lattice work of intersecting ribs which also serves as conductor of current.
The plates after being thus pasted are allowed to dry and harden, are then assembled in weak solution of H2SO4 of specific gravity 1.1 to 1.2 and are formed by passing an electric current between them. If plates are meant to be positive, they are connected up as anodes, if negative, then as cathodes. The oxygen evolved at the anode converts the lead oxide (Pb3O4) into peroxide (PbO2) and at cathode the hydrogen reduces PbO to sponge lead by abstracting the oxygen.
4. Positive Pasted Plates
Formation of positive plate involves converting lead oxide into PbO2. A high lead oxide like Pb3O4 is used for economy both in current and time, although in practice, a mixture of Pb3O4 and PbO is taken-the latter being added to assist in the setting or cementation of the plate.
5. Negative Pasted Plates
Faure process is much better adopted for making a negative rather than a positive plate. The negative material i.e. sponge lead is quite tough instead of being hard and brittle like PbO2 and moreover, it undergoes a comparatively negligible change in volume during the charging and discharging of the cell. Hence, it has no tendency to disintegrate or shed out of the grid although it does tend to lose its porosity and become dense and so lose capacity. Hence, in the manufacture of the pasted negatives, a small percentage of certain substances like powdered pumic or graphite or magnesium sulphate or barium sulphate is added to increase the porosity of the material. If properly handled, a paste made with H2SO4, glycerine and PbO (or mixture of PbO and Pb3O4) results in a very good negative, because glycerine is carbonised during formation and so helps in keeping the paste porous.
Faure plates are in more general use because they are cheaper and have a high (capacity/weight) ratio than Plante plates. Because of the lightness and high capacity/weight ratio, such plates are used practically for all kinds of portable service like electric vehicles, train lighting, car-lighting and strating etc. But their life is shorted as compared to Plante plates.
6. Structure of Faure Plates
Usually, the problem of Faure type grid is relatively simple as compared to the Plante type. In the case of Faure plates, the grid serves simply as a support for the active material and a conductor for the current and as a means for distributing the current evenly over the active material. Unlike Plante plates, it is not called upon to serve as a kind of reservoir from which fresh active material is continuously being formed for replacing that which is lost in the wear and tear of service. Hence, this makes possible the use of an alloy of lead and antimony which, as pointed out earlier, resists the attack of acid and ‘forming’ effect of current more effectively than pure lead and is additionally much harder and stiffer.
Because of the hardening effect of antimony, it is possible to construct very thin light plates which possess sufficient rigidity to withstand the expensive action of the positive active material. Simplest type of grid consists of a meshwork of veritcal and horizontal ribs intersecting each other thereby forming a number of rectangular spaces in which the paste can be pressed and allowed to set. Such a thin grid has the disadvantage that there is not much to ‘key’ in the paste and due to a great shock or vibration the pellets are easily ‘started’ and so fall out. A much better support to the active material can be given by the construction illustrated in Fig. (C) which is known as ‘basket’ type or screened grid. The paste instead of being is isolated pellets forms a continuous sheet contained and supported by the horizontal ribs of the gird. With this arrangement the material can be very effectively keyed in. Another type of grid structure used in pasted plates is shown in Fig. (D).
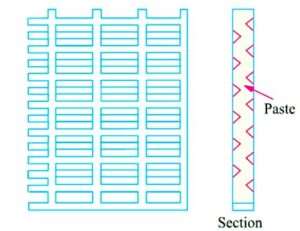
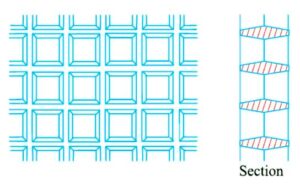
7. Comparison : Plante and Faure Plates
1. Plante plates have a longer life and can withstand rapid discharging (as in traction work) better than Faure’s.
2. They are less liable to disintegration when in use then Faure’s plates.
3. They are heavier and more expensive than Faure plates.
4. Plante plates have less capacity-to-weight ratio, values being 12 to 21 Ah per kg of plate, the corresponding values for Faure plate being 65 to 90 Ah/kg.
Read article – Units of Resistivity
Visit NCERTplanet.com for NCERT solutions and Textbook downloads